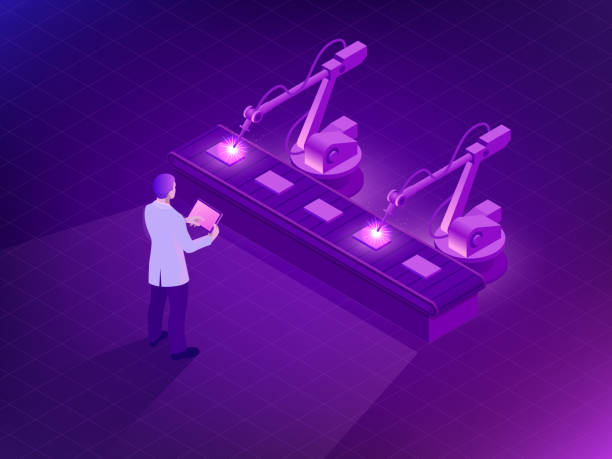
Mastering CNC Machine Maintenance: A Comprehensive Guide
Introduction
CNC (Computer Numerical Control) machines have revolutionized manufacturing processes across industries, offering precision, efficiency, and automation. However, to ensure their seamless operation and longevity, regular maintenance is crucial. In this comprehensive guide, we delve into the importance of CNC maintenance, the key components to focus on, and best practices to keep your CNC machines running smoothly.
Understanding CNC Machines
Before delving into maintenance procedures, it’s essential to understand the components and functioning of CNC machines. These machines utilize computerized controls to precisely execute predefined machining tasks, such as cutting, drilling, and shaping, on various materials. Key components include the control unit, motors, spindle, tooling, coolant system, and supporting structures.
Coolant System Maintenance: Maintain the coolant system by monitoring coolant levels, cleanliness, and pH levels. Replace coolant regularly to prevent bacterial growth, corrosion, and deterioration of machining quality. Clean coolant filters and coolant tanks to ensure efficient heat dissipation and chip evacuation.
Operator Training and Awareness: Train CNC machine operators on proper usage, maintenance procedures, and safety protocols. Empower operators to recognize warning signs of potential issues and take corrective actions promptly. Foster a culture of proactive maintenance and continuous improvement within the workplace.
Importance of CNC Machine Maintenance
Regular maintenance is paramount for maximizing the performance and lifespan of CNC machines. Neglecting maintenance can lead to decreased accuracy, frequent breakdowns, and costly repairs. Moreover, proper maintenance ensures safety in the workplace by identifying and addressing potential hazards.
Key Maintenance Procedures
Cleaning and Lubrication: Proper cleaning and lubrication are fundamental maintenance tasks for CNC machines. Dust, chips, and coolant residue can accumulate on components, affecting their performance and longevity. Regularly clean the machine surfaces, tooling, and coolant system using appropriate cleaning agents. Additionally, lubricate moving parts according to manufacturer recommendations to reduce friction and wear.
Inspection of Mechanical Components: Periodic inspection of mechanical components is essential to detect signs of wear, misalignment, or damage. Check belts, gears, bearings, and ball screws for excessive play or unusual noises. Address any issues promptly to prevent further damage and ensure optimal machine performance.
Calibration and Alignment: Accurate calibration and alignment are critical for achieving precise machining results. Regularly calibrate the machine axes, spindle, and tooling according to specified tolerances. Additionally, verify the alignment of machine components such as the spindle, table, and tool changer to maintain accuracy and consistency.
Electrical System Check: Inspect the electrical system for loose connections, damaged cables, and worn-out components. Check the control unit, servo drives, and sensors for proper functioning. Perform diagnostic tests and troubleshoot any electrical issues to prevent downtime and ensure safety.
Software Updates and Backup: Keep the CNC machine software up to date with the latest updates and patches provided by the manufacturer. Regularly backup machine programs, parameters, and settings to prevent data loss in case of system failure or corruption.
Coolant System Maintenance: Maintain the coolant system by monitoring coolant levels, cleanliness, and pH levels. Replace coolant regularly to prevent bacterial growth, corrosion, and deterioration of machining quality. Clean coolant filters and coolant tanks to ensure efficient heat dissipation and chip evacuation.
Operator Training and Awareness: Train CNC machine operators on proper usage, maintenance procedures, and safety protocols. Empower operators to recognize warning signs of potential issues and take corrective actions promptly. Foster a culture of proactive maintenance and continuous improvement within the workplace.
Conclusion
Effective maintenance practices are essential for optimizing the performance, reliability, and safety of CNC machines. By implementing a comprehensive maintenance program encompassing cleaning, lubrication, inspection, calibration, and operator training, manufacturers can maximize productivity and minimize downtime. Remember, proactive maintenance is not just a task; it’s an investment in the long-term success of your CNC machining operations.