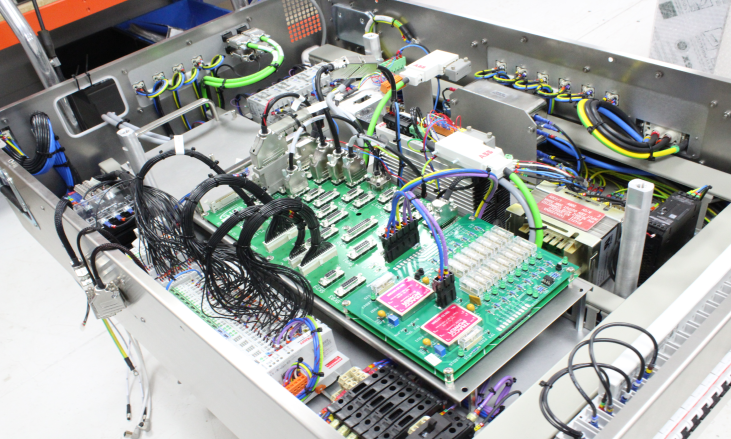
The Role of Quality Control in PCB Assembly and Box Build Assembly
When it comes to manufacturing electronic devices, ensuring quality is paramount at every step of the production process. From the PCB assembly services (Printed Circuit Board Assembly) to the box build assembly, each phase involves rigorous procedures to guarantee that the final product is reliable, durable, and performs its intended functions efficiently. While both PCB assembly and box build assembly play crucial roles in bringing a product to life, quality control (QC) is the thread that ties these stages together, ensuring that everything meets industry standards and customer expectations.
In this article, we’ll explore the importance of quality control in both PCB assembly and box build assembly. We’ll discuss the practices, challenges, and technologies that manufacturers use to uphold the highest standards of quality, ultimately leading to a superior product.
What is Quality Control in PCB Assembly?
Quality control in PCB assembly involves systematically checking that each printed circuit board is built correctly and functions as intended. The complexity of modern electronic products means that even minor defects in the PCB assembly can lead to costly malfunctions or failures down the line. This makes quality control in PCB assembly a critical process in ensuring the functionality, reliability, and performance of the final product.
Key aspects of quality control in PCB assembly include:
-
Component Placement and Soldering Inspection
-
Automated Optical Inspection (AOI): This technology visually inspects the PCB for errors such as misplaced components, soldering defects, or shorts. AOI systems capture high-resolution images and compare them with the design files to ensure everything is in place.
-
X-Ray Inspection: Often used in more complex assemblies, such as those with hidden solder joints or fine-pitch components, X-ray inspection allows manufacturers to identify internal defects that are invisible to the naked eye.
-
Soldering Quality Checks: Ensuring that the components are securely soldered to the PCB is crucial for reliability. This includes checking for cold solder joints, improper soldering, and solder bridges (unintended connections between different circuits).
-
-
Electrical Testing
-
In-Circuit Testing (ICT): This method involves testing the PCB after assembly by applying test signals to verify the functionality of individual components and circuits. It helps detect issues such as incorrect placements, open circuits, or shorts.
-
Functional Testing: Beyond just testing for electrical continuity, functional testing ensures that the PCB performs as expected in real-world conditions, including voltage and temperature variations.
-
-
Environmental Testing
-
Thermal Cycling: This test exposes the PCB to extreme temperature fluctuations to assess the thermal performance and identify potential weaknesses that may cause failures under stress.
-
Vibration Testing: Simulating physical stress to ensure that the PCB can withstand shocks and vibrations in its operational environment.
-
-
End-of-Line Testing
-
At the final stage of PCB assembly, a more comprehensive set of tests is performed to ensure that the board works as intended when integrated with other components. This includes checking for any malfunctions and ensuring all parts of the board are fully functional.
-
Quality Control in Box Build Assembly
Box build assembly goes beyond just the assembly of the PCB, incorporating additional components such as wiring, enclosures, displays, and external connectors. The quality of the box build assembly process is crucial because the final product must function as a cohesive system, with all parts working in harmony. A defect in any part of the box build can result in a malfunction or compromised product performance.
Quality control during box build assembly involves several checks to ensure the final product is functional, safe, and ready for consumer use:
-
Component Integration and Wiring
-
Visual Inspection: The integration of the PCB with other components must be carefully checked. This includes ensuring the wiring is correctly connected, components are placed in their appropriate positions, and there are no loose connections.
-
Continuity Testing: Ensuring that electrical connections between the PCB and other components (such as power supplies or displays) are intact and functioning properly. Continuity tests help identify faulty or disconnected wiring.
-
-
Enclosure Quality and Fit
-
Enclosure Inspection: The casing or enclosure of the product is inspected to ensure it fits securely around the internal components, protecting them from environmental factors such as dust, moisture, or physical damage. Any flaws in the design or fit of the enclosure could lead to malfunctions or even product failure.
-
IP Rating Compliance: For certain products, especially those used in harsh environments (such as medical or automotive electronics), the enclosure may need to meet specific Ingress Protection (IP) ratings. QC ensures the box can protect against dust and water ingress, as required.
-
-
Final System Integration and Testing
-
System-Level Functional Testing: After all the components are assembled, the final product undergoes a series of system-level tests. This includes testing the product’s overall functionality, such as power-up tests, display checks, communication functionality, and any other user interfaces. It ensures that the product works as a cohesive unit, meeting both the design specifications and customer expectations.
-
Environmental and Stress Testing: Box build assembly often involves testing for environmental factors such as temperature, humidity, and vibration to ensure the product can operate in its intended environment. For example, a consumer electronics product may be subjected to high temperatures and humidity to ensure it functions reliably under different conditions.
-
-
Compliance Testing
-
For certain industries (such as medical devices, automotive electronics, or industrial equipment), the product may need to comply with specific industry regulations or safety standards. QC testing ensures that the product meets these requirements, which could involve electromagnetic interference (EMI) testing, RoHS compliance (restriction of hazardous substances), or UL certification (Underwriters Laboratories for safety).
-
-
Packaging and Shipping
-
Packaging Integrity Check: After assembly, the final product must be packaged securely for transportation. This includes ensuring that the packaging provides sufficient protection to prevent physical damage during shipping and storage.
-
Documentation: Ensuring that all relevant documentation, such as instruction manuals, safety information, and certifications, is included in the package and that the product meets all shipping regulations.
-
Challenges in Quality Control
While quality control is essential for both PCB assembly and box build assembly, several challenges can arise during the QC process. These challenges can affect the speed, cost, and overall effectiveness of quality assurance practices:
-
Complexity of Modern Designs: As electronic products become more sophisticated, the assembly process often involves intricate designs and miniaturized components, which make quality control more difficult. Components can be harder to inspect, and small defects might not be immediately obvious.
-
Time and Cost Constraints: Manufacturers are often under pressure to reduce production time and costs, which can sometimes lead to compromises in the thoroughness of the QC process. However, cutting corners on quality control can result in defective products, customer dissatisfaction, and expensive recalls.
-
Global Supply Chain Issues: Components sourced from different regions of the world may not always meet the same quality standards. Inconsistent quality from suppliers can lead to defects in the final assembly, requiring additional testing and inspection during the assembly process.
-
Technological Limitations: While automated inspection technologies like AOI and X-ray inspection are effective at detecting certain types of defects, they still have limitations. Some defects, such as intermittent failures or issues that arise under specific operating conditions, may be harder to detect with current technologies.
Best Practices for Quality Control in PCB and Box Build Assembly
To overcome these challenges, manufacturers can adopt several best practices for quality control in both PCB and box build assembly:
-
Adopt a Comprehensive QC Strategy: Implementing a combination of automated and manual inspection methods helps ensure the highest level of accuracy and defect detection. A comprehensive strategy should cover every aspect of the manufacturing process, from component sourcing to final packaging.
-
Emphasize Early Detection: Identifying defects early in the production process is crucial. By catching problems in the PCB assembly stage, manufacturers can avoid costly issues in the box build stage.
-
Use Advanced Testing Methods: Investing in advanced testing methods such as X-ray inspection and environmental stress testing can help detect defects that may otherwise go unnoticed.
-
Supplier Quality Assurance: Establishing strict quality control standards for suppliers ensures that all incoming components meet the necessary specifications and are free from defects.
-
Continuous Improvement: Quality control is an ongoing process. Manufacturers should continuously analyze their QC processes, learn from defects, and improve their methods over time.
Conclusion
Quality control is a fundamental part of both PCB assembly and box build assembly. From ensuring that every component is correctly placed on the PCB to verifying that the final product functions as intended, QC practices play a vital role in the electronics manufacturing process. By adopting comprehensive and advanced quality control measures, manufacturers can reduce defects, improve product reliability, and deliver superior products to the market. Ultimately, quality control in both stages ensures that customers receive products that meet their needs and exceed their expectations.