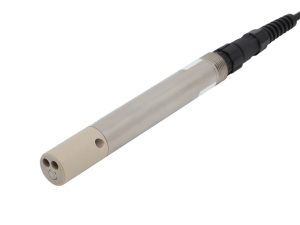
Choosing the Right Water Conductivity Meter for Industrial Applications
Water is an essential component in many industrial processes, ranging from power generation and manufacturing to chemical processing and food production. As such, maintaining optimal water quality is crucial to ensure both the efficiency of operations and the safety of products and the environment. One of the most effective ways to monitor water quality is by measuring its conductivity, which is a direct indicator of the water’s concentration of dissolved ions, such as salts, minerals, and chemicals. A Water conductivity meter is a vital tool in this process, and choosing the right one is key to ensuring the desired quality standards are met.
In this blog, we will discuss the factors to consider when selecting a water conductivity meter for industrial applications, the different types available, and how to make the best choice based on specific needs and requirements.
What is a Water Conductivity Meter?
A water conductivity meter measures the electrical conductivity (EC) of water, which is a measure of the water’s ability to conduct an electrical current. This ability is influenced by the presence of dissolved ions, such as salts, minerals, and chemicals. The higher the concentration of dissolved ions, the higher the conductivity. This measurement is crucial for determining the purity of water or detecting contaminants that could affect the industrial process.
Water conductivity meters are widely used in industries such as power generation, food and beverage, pharmaceuticals, mining, and chemical manufacturing to monitor water quality. These meters come in various models and types, from handheld portable devices to stationary meters that provide continuous monitoring.
Why Is Conductivity Important in Industrial Applications?
In industrial settings, water is often used in cooling systems, production processes, and cleaning operations. The conductivity of the water in these systems plays a significant role in ensuring proper function and efficiency. Here are several reasons why monitoring water conductivity is critical:
-
Corrosion Prevention: High conductivity levels in water can cause corrosion in pipes, machinery, and equipment, leading to maintenance issues and costly repairs. For example, in power plants, the quality of water used in cooling towers or boilers must be carefully monitored to prevent scaling and corrosion.
-
Scaling Prevention: High mineral content in water can lead to scaling, which reduces the efficiency of heat exchangers, pipes, and boilers. Monitoring conductivity allows facilities to manage water quality and prevent the build-up of unwanted mineral deposits.
-
Product Quality Control: In industries such as food and beverage or pharmaceuticals, the quality of water used in production must meet specific standards. Conductivity measurements can be used to assess whether the water is pure enough for use in manufacturing processes, ensuring that products are safe and meet regulatory standards.
-
Wastewater Management: In many industrial processes, wastewater is generated and must be treated before being discharged or reused. Conductivity meters are crucial for monitoring effluent quality and ensuring that it meets environmental regulations.
Key Factors to Consider When Choosing a Water Conductivity Meter
When selecting a water conductivity meter for industrial applications, several factors need to be considered to ensure it fits the specific needs of the operation. Below are the key elements to keep in mind:
1. Measurement Range
Different industrial applications require different conductivity measurement ranges. For example, water used in cooling towers or boilers may have high levels of dissolved solids, requiring a meter with a high conductivity range. Conversely, processes that require ultrapure water, such as in pharmaceuticals, need a meter that can measure very low conductivity levels.
Before purchasing, it is important to determine the expected range of conductivity in the water being tested. Look for a meter that can cover the full spectrum of conductivity that your process requires. Some meters have automatic range switching, while others may offer user-selectable ranges.
2. Accuracy and Precision
Accuracy is one of the most important factors when choosing a conductivity meter for industrial applications. In precise operations, such as chemical manufacturing or water treatment, even small changes in conductivity can significantly impact the process. A meter with high accuracy and precision ensures that the measurements you take are reliable, preventing operational issues and enabling you to take corrective action quickly when needed.
Consider the meter’s tolerance level and ensure it meets the accuracy required for your specific industry standards. Some industrial processes may require conductivity meters with an accuracy of ±1% or better.
3. Temperature Compensation
The conductivity of water is temperature-dependent, and conductivity measurements can vary with changes in temperature. Most industrial settings experience fluctuations in water temperature, which can affect the accuracy of conductivity readings. For this reason, choosing a meter with automatic temperature compensation (ATC) is essential.
ATC automatically adjusts the conductivity reading based on the temperature of the water, ensuring that the meter provides accurate results regardless of environmental temperature changes. This is particularly important in industries where the water temperature can vary significantly, such as in cooling towers, industrial processes, or outdoor operations.
4. Probe Type and Material
The type of probe and the materials used in its construction are essential considerations when selecting a water conductivity meter for industrial use. Different probes are suited for different applications, depending on the level of contamination, water flow, and temperature conditions. Probes made of durable materials like stainless steel or titanium are ideal for harsh industrial environments, where corrosion or wear could occur.
For example, if you’re working with water that contains aggressive chemicals or high-temperature environments, selecting a probe that can withstand these conditions is critical to ensure long-term reliability. Additionally, some probes are designed for submersion in harsh chemicals or high-pressure systems, while others are best suited for low-flow systems.
5. Portability vs. Stationary Models
Water conductivity meter come in both portable and stationary versions, and the choice between these options depends on how and where the meter will be used.
-
Portable meters are ideal for industries that require flexibility and frequent testing at various points in the system, such as in field operations or for on-the-spot testing in multiple locations. These meters are often handheld and offer convenience for mobile testing.
-
Stationary meters are designed for continuous monitoring and are often used in fixed locations where constant water quality data is needed, such as in water treatment plants, boilers, or cooling systems. These meters are usually connected to automated systems that record and track data over time.
For some operations, a combination of both portable and stationary meters might be required to ensure thorough monitoring.
6. Data Logging and Connectivity
In industrial applications, it is often essential to track water quality over time for analysis, reporting, and regulatory compliance. Many modern water conductivity meters come equipped with data logging capabilities, allowing you to store conductivity readings for later analysis.
Look for a meter with a data logging feature that enables you to record and export data easily. Some advanced models also come with Bluetooth or USB connectivity, allowing data to be transferred to a computer or cloud-based system for further analysis or reporting.
7. Ease of Calibration and Maintenance
To maintain the accuracy of your conductivity meter, it is essential to calibrate the instrument regularly. Some meters offer easy-to-use calibration options, which are particularly useful in industries where frequent recalibration is necessary.
Consider a meter that simplifies the calibration process and ensures minimal downtime for maintenance. Additionally, choosing a model with easy-to-replace probes and accessories can help extend the meter’s lifespan and reduce overall maintenance costs.
Types of Water Conductivity Meters for Industrial Applications
-
Handheld Conductivity Meters: These are portable meters ideal for field testing or spot checks. They are often used in outdoor applications like water sampling from rivers, lakes, or reservoirs.
-
Inline Conductivity Meters: These are stationary meters installed directly into the water system. They are used for continuous monitoring of water quality and are commonly used in industries like power generation, wastewater treatment, and chemical processing.
-
Bench-Top Conductivity Meters: These meters are designed for laboratory settings where high accuracy and repeatability are required. They are typically used for analyzing water samples in controlled environments.
-
Wireless and Smart Meters: These advanced meters allow for remote monitoring, data logging, and cloud-based analysis. They are ideal for facilities that require continuous data collection and real-time analysis for decision-making.
Conclusion
Selecting the right water conductivity meter for industrial applications is a crucial step in maintaining optimal water quality and ensuring the smooth operation of industrial processes. By considering factors such as measurement range, accuracy, temperature compensation, probe material, and data logging features, you can choose the meter that best meets the needs of your specific application.
Whether you need a portable meter for fieldwork or a stationary model for continuous monitoring, the right conductivity meter will help you detect contamination, prevent scaling and corrosion, and ensure the overall efficiency and safety of your industrial operations. By investing in the right tools, businesses can reduce operational costs, maintain product quality, and stay compliant with environmental regulations, all while contributing to a more sustainable future.